The Blog

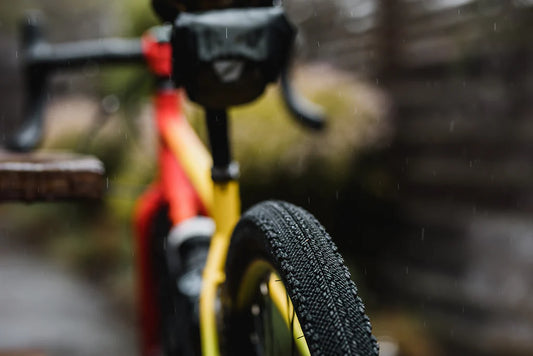
In support of a Tires-First approach
So you're here to buy wheels? Great, but not until we have a conversation about tires.
In support of a Tires-First approach
So you're here to buy wheels? Great, but not until we have a conversation about tires.
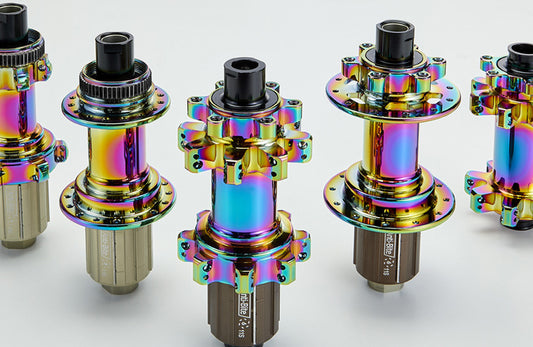
Personal identity and hub color
We don't just ride bikes - we're "cyclists." Identity influences our equipment choices not just for how we perform, but also how we feel. (It's why colored hubs are so popular.)
Personal identity and hub color
We don't just ride bikes - we're "cyclists." Identity influences our equipment choices not just for how we perform, but also how we feel. (It's why colored hubs are so popular.)
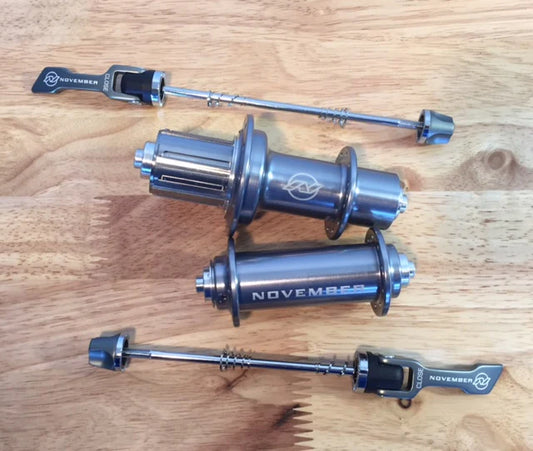
White Industries buys Rolf Prima / Astral, and ...
Industry consolidation that hits close to home, prompting some reflections on channel evolution over the past few years.
White Industries buys Rolf Prima / Astral, and ...
Industry consolidation that hits close to home, prompting some reflections on channel evolution over the past few years.
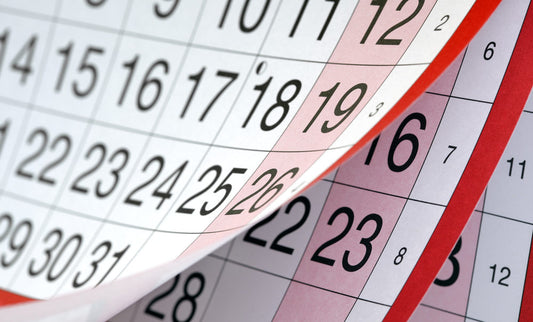
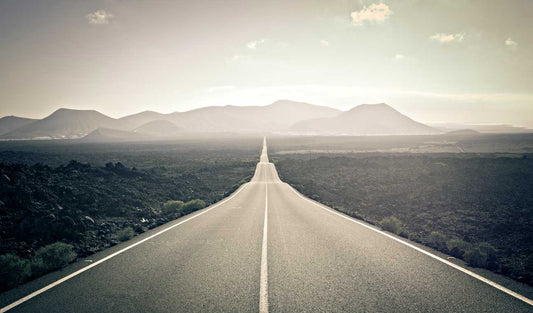
Some good news on availability, lead times and ...
What a long road it's been to get back to normal. But we're almost there.
Some good news on availability, lead times and ...
What a long road it's been to get back to normal. But we're almost there.